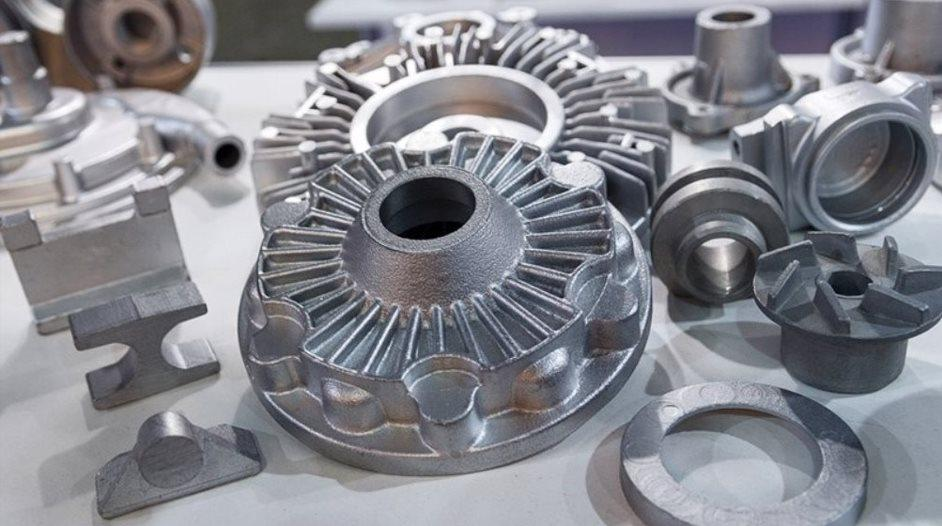
Die casting is a highly efficient and widely used metal manufacturing process that enables the mass production of complex and high-precision components. From automotive parts to electronic enclosures, die casting offers strength, durability, and consistency. However, the quality of the final product heavily depends on selecting the right die casting manufacturer.
A reliable die casting manufacturer must offer advanced technology, precision, cost-effective solutions, and quality assurance. This article explores the key factors to consider when choosing a die casting supplier, the benefits of die casting, and the industries that rely on this process.
What Is a Die Casting Manufacturer?
A die casting manufacturer specializes in producing metal components using high-pressure casting techniques. They design molds, melt metals, inject them into molds at high pressure, and carry out post-processing treatments to meet industry specifications.
There are two main die casting methods:
- Hot chamber die casting – Ideal for low-melting metals like zinc and magnesium.
- Cold chamber die casting – Suitable for high-melting metals like aluminum and copper.
Manufacturers may focus on specific materials or industries, making it crucial to choose one that aligns with your project needs.
Factors to Consider When Selecting a Die Casting Manufacturer
1. Industry Experience and Reputation
A manufacturer’s experience directly affects product quality. Established die casting manufacturer have extensive expertise, advanced equipment, and proven quality control processes. Look for companies with a strong reputation in the market and positive customer reviews.
2. Material and Alloy Selection
The choice of metal affects strength, weight, and durability. A good manufacturer should offer a range of materials, including:
- Aluminum alloys – Lightweight, corrosion-resistant, and strong.
- Zinc alloys – Ideal for detailed parts with high precision.
- Magnesium alloys – Lightweight yet durable.
- Copper and brass – Excellent conductivity and wear resistance.
3. Advanced Manufacturing Technology
Modern die casting relies on automated machinery, computer-controlled processes, and high-precision tools. A manufacturer that invests in cutting-edge technology can produce superior parts, reduce defects, and increase production speed.
4. Quality Assurance and Certifications
Certifications indicate strict quality control and compliance with industry standards. Look for manufacturers with:
- ISO 9001 – General quality management certification.
- IATF 16949 – Automotive industry certification.
- AS9100 – Aerospace quality standard.
5. Production Capacity and Lead Time
The manufacturer should have the capacity to handle your order size efficiently. Fast production and reliable lead times prevent delays and ensure timely delivery of components.
6. Surface Finishing and Secondary Processes
A good manufacturer offers finishing services like:
- Anodizing – Increases corrosion resistance.
- Powder coating – Enhances durability and appearance.
- Polishing and plating – Provides a smooth, aesthetic finish.
7. Cost-Effectiveness and Pricing Transparency
The right manufacturer offers competitive pricing without compromising quality. Look for detailed cost breakdowns covering:
- Tooling costs
- Material expenses
- Production and finishing costs
Transparent pricing helps avoid hidden charges.
8. Customer Support and Technical Assistance
Reliable manufacturers provide clear communication, expert technical guidance, and responsive support. They should assist with:
- Design optimization
- Material selection
- Process improvements
Advantages of Choosing a Reputable Die Casting Manufacturer
1. High Precision and Complex Geometries
Experienced manufacturers produce parts with tight tolerances and intricate details, ensuring components meet exact specifications.
2. Fast and Efficient Production
Die casting allows for rapid manufacturing, making it ideal for mass production without compromising quality.
3. Consistency and Uniform Quality
A skilled manufacturer ensures every part is identical, reducing errors and minimizing material waste.
4. Strength and Durability
Die-cast parts have high tensile strength and excellent mechanical properties, making them suitable for demanding applications.
5. Cost-Effectiveness in Large Volumes
Once the mold is created, per-unit costs decrease, making die casting an economical choice for bulk production.
Industries That Depend on Die Casting
1. Automotive Industry
- Used for engine components, transmission housings, brackets, and wheels.
- Helps reduce vehicle weight while maintaining strength.
2. Aerospace and Aviation
- Die-cast parts offer high precision and lightweight properties for aircraft.
- Used in landing gear, structural components, and brackets.
3. Electronics and Telecommunications
- Die casting is used for mobile phone casings, heat sinks, connectors, and enclosures.
- Ensures good heat dissipation and durability.
4. Medical Equipment
- High-precision die casting ensures biocompatible and accurate medical devices.
- Used in diagnostic equipment, imaging machines, and surgical tools.
5. Industrial Machinery and Robotics
- Die-cast parts provide strength, durability, and lightweight properties.
- Used in pumps, hydraulic systems, and automation components.
Die Casting Process Overview
Step 1: Mold Creation
- A high-quality steel mold (die) is designed for mass production.
- The mold is engineered for precision and durability.
Step 2: Metal Melting
- The chosen metal is melted in a furnace at controlled temperatures.
Step 3: High-Pressure Injection
- The molten metal is forced into the mold at high pressure, ensuring it fills every detail.
Step 4: Cooling and Solidification
- The metal cools and hardens into the desired shape.
Step 5: Ejection and Trimming
- The solidified part is ejected from the mold.
- Excess material is trimmed for a clean finish.
Step 6: Surface Treatment and Quality Control
- Finishing processes are applied for enhanced durability and aesthetics.
- Quality inspections ensure zero defects.
Future Trends in Die Casting Manufacturing
1. Automation and Robotics
- AI and robotics enhance precision and efficiency.
2. Sustainable Manufacturing
- Increased focus on eco-friendly production and material recycling.
3. 3D Printing for Rapid Prototyping
- Additive manufacturing speeds up tooling and prototyping.
4. Smart Manufacturing and IoT
- Sensors and data analytics optimize production efficiency.
Conclusion
Selecting the right die casting manufacturer is essential for ensuring high-quality, cost-effective, and precise metal components. A reliable manufacturer should offer advanced technology, material expertise, quality assurance, and competitive pricing.
Die casting is a key process for industries like automotive, aerospace, electronics, and industrial machinery, thanks to its high efficiency, durability, and complex design capabilities. By choosing a trusted manufacturer, companies can achieve consistent, high-performance components that meet industry standards.