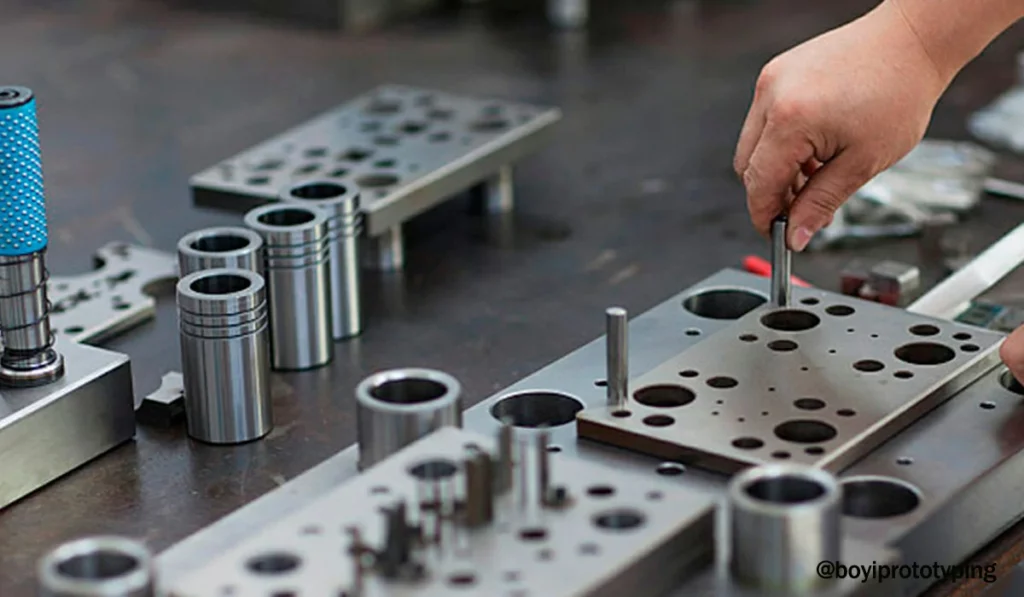
Die tooling manufacturers play a crucial role in various industries, providing essential components used in stamping, molding, and forming materials into precise shapes. These manufacturers design and produce dies, which are specialized tools used in cutting, shaping, and forming metals, plastics, and other materials. Their products are essential in industries such as automotive, aerospace, electronics, medical, and consumer goods manufacturing.
This article explores the importance of die tooling manufacturers, different types of dies, manufacturing processes, challenges, and technological advancements in the industry.
Importance of Die Tooling Manufacturers
Die tooling manufacturers are at the core of precision manufacturing, ensuring that products meet strict industry standards while optimizing efficiency and reducing costs.
1. Ensuring High Precision
Manufacturers rely on die tooling to produce consistent, high-accuracy components that meet tight tolerances required in various industries.
2. Enhancing Production Efficiency
High-quality dies improve manufacturing efficiency by automating processes, reducing manual labor, and minimizing errors, leading to faster production cycles.
3. Reducing Material Waste
With precise tooling, manufacturers can reduce material waste, cutting down on production costs and promoting sustainable manufacturing practices.
4. Improving Product Quality and Durability
die tooling manufacturers create dies that ensure structural integrity, leading to more durable, high-performance products in sectors such as automotive, aerospace, and medical devices.
Types of Die Tooling
Die tooling manufacturers produce various types of dies, each designed for specific applications.
1. Cutting Dies
Cutting dies are used to trim, shear, or punch materials into the desired shape. Examples include:
- Blanking dies – Cut flat shapes from metal sheets.
- Trimming dies – Remove excess material from components.
- Piercing dies – Create holes and perforations.
2. Forming Dies
These dies shape materials without cutting, allowing them to be bent, stretched, or embossed into the required design. Common types include:
- Bending dies – Form metal sheets into angles or curves.
- Drawing dies – Stretch materials into deep, hollow shapes such as cans and pipes.
- Embossing dies – Create raised or recessed designs on surfaces.
3. Progressive Dies
Progressive dies perform multiple operations in a single process, such as cutting, bending, and forming, improving production speed and reducing labor costs.
4. Compound Dies
These dies execute multiple cutting operations in one stroke, enhancing efficiency in high-volume manufacturing.
5. Injection Molding Dies
Used for plastic parts manufacturing, these dies create complex shapes with high accuracy and repeatability.
6. Extrusion Dies
Extrusion dies help in shaping metals, plastics, and rubber materials by forcing them through a mold to achieve a continuous profile.
The Manufacturing Process of Die Tooling
Die tooling manufacturers follow highly precise processes to create durable and accurate dies. The production process includes several key steps:
1. Design and Engineering
Manufacturers use computer-aided design (CAD) software to create detailed blueprints for die production.
2. Material Selection
High-performance materials such as hardened steel, tungsten carbide, and aluminum are chosen based on durability and application requirements.
3. CNC Machining
Computer Numerical Control (CNC) machining is used to cut and shape die components with extreme precision. CNC technology ensures high accuracy and repeatability.
4. Electrical Discharge Machining (EDM)
EDM is used for intricate die components, allowing manufacturers to cut complex shapes in hardened materials using electrical discharges.
5. Heat Treatment and Surface Finishing
Dies undergo heat treatment to improve hardness and durability. Surface finishing techniques such as coating, polishing, and plating enhance the lifespan of the dies.
6. Inspection and Quality Control
Manufacturers perform rigorous testing and inspections to ensure that each die meets industry standards and client specifications.
Applications of Die Tooling
Die tooling manufacturers cater to multiple industries, supplying essential components for mass production and high-precision applications.
1. Automotive Industry
Die tooling is used in manufacturing engine parts, car body panels, transmission components, and structural elements.
2. Aerospace Industry
Aircraft manufacturers rely on die tooling for lightweight, high-strength components, ensuring aircraft safety and performance.
3. Electronics and Consumer Goods
Die tooling enables the production of circuit boards, semiconductor components, and metal casings for electronic devices.
4. Medical Equipment Manufacturing
Medical manufacturers use die tooling to produce surgical instruments, implants, and high-precision medical devices.
5. Industrial Machinery and Heavy Equipment
Precision die tooling is used to manufacture machine parts, gears, and industrial tools required for high-load applications.
Challenges Faced by Die Tooling Manufacturers
Despite their importance, die tooling manufacturers face several challenges, including:
1. High Production Costs
The use of specialized materials, high-end equipment, and skilled labor increases production costs, making die tooling an expensive process.
2. Wear and Tear of Dies
Due to high-pressure manufacturing, dies experience wear and must be regularly maintained and replaced.
3. Maintaining Tight Tolerances
Manufacturing components with precise dimensions and tolerances requires advanced quality control methods and high-tech machinery.
4. Shortage of Skilled Workers
The die tooling industry demands highly skilled engineers and machinists, and the shortage of trained professionals affects production efficiency.
Innovations in Die Tooling Manufacturing
Technological advancements are transforming die tooling, making manufacturing more efficient and cost-effective.
1. Automation and Robotics
The use of robotic systems and AI-driven automation speeds up production, reduces errors, and improves consistency.
2. 3D Printing for Prototyping
3D printing allows manufacturers to create rapid prototypes of dies, reducing lead times and development costs.
3. Advanced Coatings for Longer Tool Life
Innovative coatings such as ceramic and diamond-like carbon (DLC) coatings improve die durability and wear resistance.
4. AI in Quality Control
Artificial intelligence helps in real-time defect detection, improving product quality and minimizing rework costs.
5. Sustainable Manufacturing Practices
Manufacturers are implementing eco-friendly processes, using recyclable materials and energy-efficient machining to reduce environmental impact.
Conclusion
Die tooling manufacturers are essential in modern industrial production, providing high-precision tools for various industries such as automotive, aerospace, electronics, medical, and industrial manufacturing. Their products ensure accuracy, efficiency, and consistency in mass production and custom fabrication.
With advancements in CNC machining, AI-driven quality control, and automation, the die tooling industry continues to evolve, making production more precise and cost-effective. Despite challenges such as high costs, wear and tear, and skilled labor shortages, continuous innovations are improving durability, efficiency, and sustainability in die tooling manufacturing.
As industries demand higher precision and faster production, die tooling manufacturers will continue to play a pivotal role in shaping the future of manufacturing.